New possibilities when robots move freely
Robots today require static environments to operate efficiently, navigating with the help of wires in the floor or reflectors on the walls. But this is something that researchers at Örebro University want to change. In an article in The International Journal of Robotics Research, they are describing a system that allows robots to navigate reliably despite changes in their environment. The objective is to enable robots to move freely and operate in environments with constant activity.
– With our system, robots or in this case autonomous forklift trucks are able to navigate without the need to install wires or reflectors despite changes in their environment over time. They are able to find new paths if the one they were previously using has been blocked. This may be easy for us humans, but for robots it is a huge challenge, says Achim Lilienthal, a robotics researcher at Örebro University.
If robots are able to perceive and respond to what is going on around them, they can move freely and operate more efficiently in environments where people may cross their paths or in warehouses where goods are being shifted constantly. In the future, they could then be used to a much greater extent for example within industry and agriculture, but also in mines or at airports.
Quicker and more reliable
To enable robots to see what is going on around them, researchers are creating 3D maps. With a map that receives constant updates, the robot will be able to negotiate challenging environments. The new mapping technology now presented by the Örebro researchers is quicker, more reliable and more precise than before.
The technology combines two different methods – Normal Distribution Transform, NDT, and Occupancy Grid Maps, OM. NDT is used to create three-dimensional maps by compressing the many measurement points, 500,000 per second, that are reflected off various objects. Instead of saving all these points separately, they are compressed and represented as ellipsoids, i.e. as oval shapes rather than as separate points, which are stored in the robot's memory.
In a dynamic environment
– If you were to save all measurement points, it would quickly fill up the memory space. In addition, the robot would need a lot of time to compare new measurement data to all the points stored in the memory, says Achim Lilienthal.
To take it bearings the robot must all the time compare what it sees with what it has come across before.
– Especially in changing environments, our solution combines the best of two worlds. NDT makes it possible for large quantities of data to be saved efficiently while OM brings stability and robustness.
– We have had the opportunity to test the system in a warehouse for a considerable period of time and our findings show that the system is stable and consistent. NDT-OM produces 3D maps with which the robot is able to navigate dynamic industrial environments, says Achim Lilienthal.
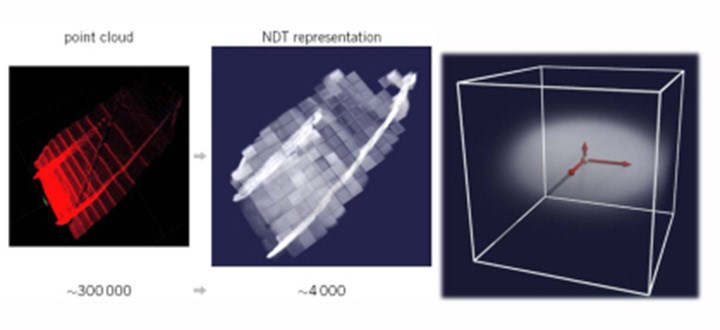
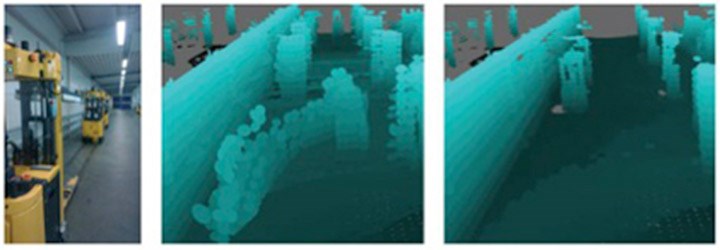
Text: Linda Harradine
Translation: Charlotta Hambre-Knight
Photo: Therése Andersson, Örebro University